Reconext
Grapevine, Texas, United States
CONDENSED CASE STUDY
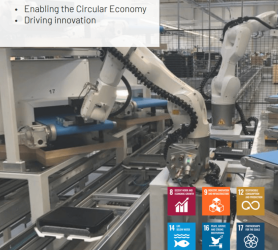
IMPACT
MODEL
CYCLE PHASE

- INT-PSN1
Circular Case Studies by Circular Regions licensed under CC BY-NC-ND 4.0

STATUS & TIMELINE
Teleplan foundation | 01/1983 | |
Teleplan & Clover Rebranding | 09/2020 |
DESCRIPTION
Reconext delivers solutions that enable customers to meet their objectives by optimizing the value of returned electronic devices for customers with the goal of 100% reuse of all materials. Headquartered in Dallas, Reconext has a broad global footprint, including 18 service centers across the Americas, Asia Pacific and Europe, that offer cost-effective, innovative supply chain solutions for customers worldwide. The Company has several thousand employees globally, with strong technical expertise, deep engineering credentials and a shared commitment to advanced component reclamation, device repair and refurbishment. Reconext’s end-to-end aftermarket lifecycle services include returns management & fulfillment, testing & grading, repair & refurbishment, asset recovery and trade-in & buy-back.
Reconext use Al to help provide after market and lifecycle care services to keep electronics products in use, such as managing reverse logistics, screening and testing, and repairing and refurbishing of used electronic devices. Reconext uses Al to generate objective, consistent and cost effective grading of used devices, by assessing the external or cosmetic condition of the devices and determining if they can be reused or resold, whether they need to be repaired, refurbished or recycled, and their market value. Reliably knowing the condition of a device can be key for consumers to accept a used device.
As a services company, their mission is to deliver solutions that enable the customers to meet their objectives by optimizing the value of returned electronic devices for the customers with the goal of 100% reuse of all materials. They accomplish this through continuous innovation in repair, remanufacturing, refurbishment, reclamation and remarketing technologies.
In 2019 alone we extended the life of 23.7 million used devices, enabling our customers to avoid 1.31 million tCO2e emissions from new manufacturing. Through innovative aftermarket service solutions, we help to minimize the environmental impact from our operations and those of our customers and partners. We provide support to our customers in their evolution towards a more circular economy model, where the reuse of devices, parts and material is paramount.
Login to download a .pdf